De tien meest gemaakte fouten door green belts
Tijdens en na hun opleiding
Het volgen van een Green Belt geeft deelnemers de kennis en vaardigheden om zelfstandig verbeterprojecten aan de hand van Lean of Lean Six Sigma uit te voeren. In de praktijk zien dat veel Green Belts bij hun verbeterprojecten nog in veelvoorkomende valkuilen stappen. We hebben de 10 meest voorkomende voor je op een rijtje gezet.
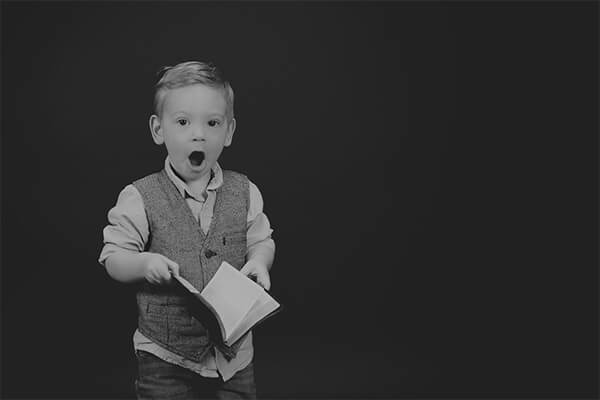
De lijst is niet gebaseerd op wetenschappelijk onderzoek, maar een verzameling van wat wij zien gebeuren in de praktijk.
#1: Beginnen met te grote verwachtingen
Niets is zo demotiverend als teleurstelling. Een Green Belt in Lean of Lean Six Sigma Green Belt wordt gaandeweg de opleiding steeds enthousiaster over de mogelijkheden. Zij creëren voor zichzelf een beeld van een organisatie die volledig werkt volgens de filosofie. En ze denken dat ze na de opleiding dit beeld kunnen realiseren, vaak binnen een aantal weken.
De realiteit is weerbarstiger. Om projecten te starten en succesvol af te ronden zijn tijd en middelen nodig. En tijd en middelen zijn niet oneindig. Green Belts moeten geholpen worden bij het maken van keuzes voor verbeterprojecten en deze moeten vaak flink aangescherpt worden. Tegelijkertijd moeten de verwachtingen getemperd worden om teleurstelling te voorkomen.
#2: Het niet voldoende plannen van tijd en middelen voor een project
Een Green Belt in opleiding komt vaak aan met gedetailleerde schema’s met mijlpalen, maar heeft vaak niet de benodigde tijd en middelen zorgvuldig overwogen. Ook al komen bepaalde richtingslijnen voor in enkele organisaties, zoals: “40% van de werktijd zal worden besteed aan een Green Belt project”, waarbij het soms toch kan voorkomen dat dit in een week 150% bedraagt van de gebruikelijke 40-urige werkweek om bepaalde kritische slagen te kunnen maken.
3#: Het niet verkennen van alle theoretische bronnen
Een Lean training of Lean Six Sigma training is vaak intensief. Deelnemers spenderen daarom – naast de verplichte onderdelen – niet genoeg tijd om extra theorie tot zich te nemen met betrekking tot Lean of Lean Six Sigma. We zien dat er steeds meer opleiders ontstaan die sterk verkorte – of zelfs E-Learning only – Green Belt opleidingen aanbieden. De ervaring leert dat dit niet voldoende is om de stof echt te begrijpen of om als Green Belt aan de slag te kunnen. Deze opleidingen beperken zich vaak tot welbekende sheets, tools en voorbeelden.
Om als Green Belt echt een bijdrage te doen aan de resultaten van de organisatie, is het essentieel om de theorie te doorgronden en kennis hiervan zo ver mogelijk uit te diepen.
#4: Het vroegtijdig bedenken van oplossingen voor het project van start is gegaan
Deze fout wordt veelvuldig gemaakt door de manier waarop projecten in het algemeen worden uitgevoerd binnen organisaties waar Green Belts werken. In sommige organisaties, is het een teken van zwakte om niet direct een oplossing te kunnen bedenken voor een probleem. Een praktijkvoorbeeld is een organisatie waar een medewerker niet een onderwerp kon aankaarten in het management teamoverleg voordat hij met verbeteropties kwam en deze aanleverde.
Binnen Lean en Lean Six Sigma, is het zaak om allereerst het probleem te doorgronden, te meten, en te analyseren voordat er überhaupt gedacht wordt in verbeteroplossingen. Het vroegtijdig focussen op oplossen is een veelvoorkomende uitdaging voor veel recent opgeleide Belts.
#5: Het niet evalueren van de gestelde doelen
10% is een magisch getal. Een nieuwe Green Belt in Lean of Lean Six Sigma Green Belt zal een verbetering van 10% vaak al doel gebruiken voor een verbeterproject. Wanneer we vragen naar de herkomst van die 10%, blijft een doordacht antwoord uit. Die 10% klinkt gewoon goed, ze vragen zich niet af of 10% wel genoeg is. Of misschien onhaalbaar.
Het is voor nieuw opgeleide verbeterprofessionals zaak om zichzelf te motiveren om weloverwogen keuzes te maken en gefundeerde doelstellingen op te stellen.
#6: De afkeer om in kwantitatieve termen te denken
Het is voor veel mensen eng om in kwantitatieve termen te praten. Ze spraken dan vaak over zaken als het verhogen van de klanttevredenheid, het verhogen van de kwaliteit of het tegengaan van verspilling, maar ze maken deze niet concreet. Het concreet maken van deze zaken bijvoorbeeld door te stellen dat het aantal klachten met 30% verlaagd moet worden, maakt dat de verbeterprojecten gericht en meetbaar worden.
Voor veel organisaties is dit een uitdaging omdat ze gewend zijn om alleen financiële data te kwantificeren. Maar voor het succes van de verbeterprojecten dienen dus alle doelstellingen concreet en meetbaar gemaakt te worden.
#7: Veronderstellen dat data uit metingen niet voldoende aanwezig zal zijn om een project uit te voeren
Dat data niet beschikbaar is in de vorm die je graag wilt, betekent niet dat er geen data is. En toch horen we Green Belts vaak zeggen dat ze niet beschikken over de nodige data. Zoals in het volgende simpele voorbeeld:
Een projectgroep wil graag de doorlooptijd reduceren voor wijzigingsverzoeken in vliegtuigmotorsoftware in militaire vliegtuigen. De huidige doorlooptijd was 46 maanden. Het team bracht hen de veertig meest recentelijk voltooide wijzigingsverzoeken. Het commentaar hierop was: “We hebben een groot probleem. We moeten ervoor zorgen dat de distributeurs nog sneller reageren op verzoeken, maar we hebben geen data om dit op te meten. De documenten waarover de distributeurs beschikten lieten zien dat elke wijzigingsverzoek gepaard ging met een 26-stappenschema om wijzigingen gestructureerd in te voeren. De distributeurs zelf namen vier weken van de totale doorlooptijd voor hun rekening om de eigen twee stappen te doorlopen om wijzigingen door te voeren. De overige 45 maanden waren dus benodigd om de overige 24 stappen te doorlopen, voordat distributeurs hun deel van het wijzigingsproces hadden verricht.
Geen data? In feite was de data aanwezig, maar is door een simpele conversie (weken naar maanden) op te lossen. Deze eenvoudige misverstanden en veronderstellingen worden overigens nog steeds gemaakt in de praktijk.
#8: Het willen overslaan van stappen
Of er nu gewerkt wordt met Lean of met Lean Six Sigma, de uitdaging blijft om niet overhaast door stappen heen te gaan, of ze zelfs over te slaan. In het geval van DMAIC zien we vaak dat deelnemers zo snel mogelijk naar de Measure en Analyse fase willen. Hierbij wordt de Define fase niet goed uitgediept. Hetzelfde fenomeen zien we in het geval van Lean, waarin het definiëren van het probleem en het onderzoeken van de bronoorzaken te vluchtig gedaan wordt.
Het gevolg is dat sommige projecten volledig opnieuw gedaan moeten worden, omdat de tegenmaatregelen onvoldoende afgestemd zijn op de bronoorzaak. En daardoor niet het gewenste resultaat bewerkstelligen.
#9: Vooroordeel dat de methode niet toepasbaar is
Voor een aanzienlijk deel van de deelnemers geldt dat de deelname aan een Green Belt in Lean of Lean Six Sigma Green Belt opgelegd wordt door de werkgever. In dat geval is er een Lean of Lean Six Sigma programma actief in de organisatie en moet de deelnemer hierop aansluiten. Vanwege de arbeidsrelatie kan hier geen weerstand tegen uitgesproken worden.
Dat betekent niet dat er geen weerstand is, die wordt alleen op een andere manier geuit. We zien dan dat deelnemers beweren dat Lean of Lean Six Sigma niet toegepast kan worden binnen hun werkomgeving. Beide methodes hebben de waarde al bewezen binnen iedere werkomgeving, waardoor het vooroordeel ongegrond is.
Een goede trainer of coach laat deze deelnemers dan ook binnen no-time ervaren hoe de methode wél kan werken. Waarna al snel alle weerstand verdwijnt en de deelnemer bevlogen aan de slag gaat. Binnen en zelfs buiten hun eigen werkomgeving.
#10: Teveel focussen de tools
Lean en Lean Six Sigma hebben beide beschikking over een enorme hoeveelheid tools. Van visgraatdiagram tot RACI. Deze tools zijn ter ondersteuning van het succes van het verbeterprogramma, maar zijn nooit een doel op zich.
We zien dat er direct verband is tussen de kwaliteit van de opleiding, trainer en afhankelijkheid van de tools. Nog teveel opleiders leren de deelnemers enkel hoe ze de tools moeten inzetten, zonder de leidende principes echt te doorgronden.
Door tijdens de training te focussen op de leidende principes en de toepassingen daarvan, volgen de tools vanzelf. Hiermee borgt de trainer dat de deelnemers na afloop van de training echt zelfstandig aan de slag kan met Lean of Lean Six Sigma. De ultieme versneller hiervan is het uitvoeren van een praktijkopdracht tijdens de opleiding.