Kanban methode
Overzicht, flow en Just In Time
Kanban is samen met Kaizen en 5S één van de meest bekende principes binnen het Toyota Production System en Lean. Het betekent vrij vertaald “Visuele kaart” en dat dekt eigenlijk de lading vrij goed. In essentie is Kanban een methode om werkprocessen en voorraad inzichtelijk te maken. Het draagt bij aan het creëren van flow en is een belangrijk onderdeel van het Just in Time principe.
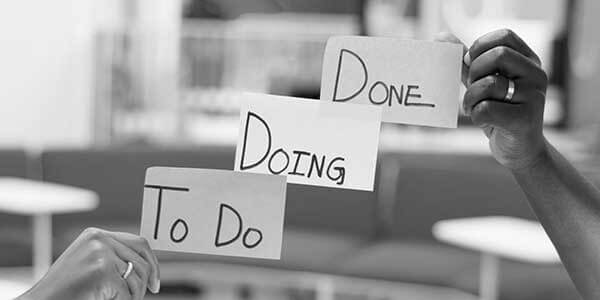
De kanban methode gaat alleen wel iets verder dan alleen het visualiseren van werkprocessen en werkvoorraad. Door de onderliggende principes goed toe te passen, heeft de methode een belangrijke rol in het continu verbeteren van het werk en de werkprocessen.
De oorsprong van Kanban
Kanban is ontwikkeld door Taiichi Ohno, één van de grondleggers van wat we vandaag de dag kennen als Lean. Hij haalde zijn inspiratie hiervoor uit een supermarkt. Het viel hem op dat sommige supermarkten een effectieve methode hadden om de vakken goed bevoorraad te houden. Zij zorgden dat de vulling van de vakken aangepast was aan de verwachting van de verkoop van de producten. Niet teveel vulling en niet te weinig. Het gevolg is dat klanten alleen kochten wat ze echt nodig hadden, omdat ze zeker wisten dat er altijd genoeg voorraad zou zijn. Er ontstond hier een natuurlijke balans tussen vraag en aanbod.
Zes leidende principes van Kanban
Binnen het kanbansysteem worden zes leidende principes gehanteerd. Deze principes – of kenmerken – worden veelal gebruikt als stappenplan om Kanban vorm te geven.
- Visualiseer de workflow: De basis van de methode is het visualiseren van de workflow. Hier werd in origine een fysiek bord voor gebruikt. Maar tegenwoordig zien we steeds vaker dat hier digitale oplossingen voor gebruikt worden. Bij de visualisatie is het van belang dat alle teamleden hieraan bijdragen en dat ze het eens zijn over welke werkzaamheden – of type werkzaamheden – opgepakt worden.
- Beperk de werkzaamheden: Binnen Kanban wordt er vaak gesproken over ‘Work in Progress’, oftewel het werk waar op dat moment aan gewerkt wordt. Door de hoeveelheid ‘work in progress’ te beperken, wordt er voor gezorgd dat werkzaamheden afgemaakt worden voordat er aan een nieuwe taak wordt begonnen. Heel praktisch bepaalt het team hier hoeveel werk ze tegelijkertijd kunnen uitvoeren.
- Beheer de workflow: Zodra er een WIP-limiet is bepaald, kan de de workflow ingericht en beheerd worden. De bedoeling van Kanban is dat items eigenlijk nooit stilstaan op het bord, ze zijn continu in beweging.
- Maak heldere afspraken: De basis van het succes van Kanban ligt in de afspraken die er gemaakt worden over de WIP-limiet, wanneer taken als ‘klaar’ beschouwd worden en wanneer een nieuwe taak wordt gestart. Vaak worden deze regels verwerkt op het kanbanbord. Zoals voor vrijwel alle afspraken die tussen mensen gemaakt worden is hierbij niet zozeer de inhoud van de afspraak het meest belangrijk, maar de mate waarin teamleden zich hier aan houden en elkaar er op aan kunnen spreken.
- Zorg voor feedbackloops: Binnen Kanban wordt gestreefd naar het continu verbeteren van de productiviteit. Om dit te bewerkstellingen worden er feedbackloops geïmplementeerd. De frequentie kan per team verschillen.
- Evalueer en verbeter: Door alle bovenstaande stappen te doorlopen wordt er een structuur aangebracht die help bij het continu verbeteren van de manier waarop het team werkt. Teams die werken aan de hand van de kanban methode merken dat ze stapsgewijs blijven verbeteren door te leren en te experimenteren.
Zelf aan de slag met Kanban?
Kanban is – net als andere bekende begrippen binnen Lean Management – relatief eenvoudig toe te passen. Je kunt al een begin maken met een whiteboard en post-its. De meest eenvoudige manier om is om het whiteboard op te delen in 3 kolommen: To Do, Doing, Done. Let er wel op dat de taken in de Doing kolom ook echt de taken zijn waar het team mee bezig is. Taken die nog niet af zijn maar waar het team ook niet mee bezig is, hebben geen plek in de Doing kolom. Die moeten ofwel terug naar To Do, of er moet een extra kolom gemaakt worden.
Laten we bijvoorbeeld het schrijven van een boek als voorbeeld nemen. Voor ieder hoofdstuk is een kaartje gemaakt op het kanban-bord. Wanneer er een hoofdstuk geschreven is, wordt dit aan een copywriter gestuurd die de eindredactie doet. De taak van het schrijven van het hoofdstuk is dan dus niet af, maar er is ook niemand in het team meer mee bezig. Het is dan logisch om een extra kolom toe te voegen, bijvoorbeeld: ‘Eindredactie’. Deze kolom gaat dan dus niet van de capaciteit van het team af, maar er is wel direct inzichtelijk dat er nog aan gewerkt wordt.
Een whiteboard is handig als het team iedere dag samenwerkt op één locatie. Maar in de huidige tijd is het veelal handiger om een online kanban-bord op te zetten. Tools als Trello, Microsoft Planner en Mural worden hier veelvuldig voor gebruikt.
Kanban en Agile
Kanban en Agile kennen aardig wat overeenkomsten. Het is dan ook niet voor niets dat Kanban een plek heeft in het Scaled Agile Framework. Met name het Scrum Framework lijkt op het eerste oog veel overeenkomsten te hebben met het kanbansysteem. Binnen Scrum worden projecten opgedeeld in kleine taken die iteratief worden uitgevoerd. Het scrumteam bepaalt wanneer het werk klaar is en hoeveel werk ze per iteratie kunnen verzetten. Scrumteams maken onderlinge afspraken over hoe ze het werk doen en evalueren het werk en het proces. Allemaal elementen die ook in Kanban zijn opgenomen.
Toch zijn er ook verschillen tussen Kanban en Agile. Het grootste verschil ligt in de aard van het werk. Kanban is gebaseerd op een werkomgeving waar processen continu zijn. Het systeem is ingericht op een werkvoorraad die vanzelf aangevuld wordt. Dit is afhankelijk van de vraag vanuit de organisatie of andere processen. Agile – en specifiek Scrum – is meer gericht op een projectmatige aanpak. De projecten worden opgedeeld in kleinere taken die een prioriteit krijgen binnen het grotere geheel. Het doel is om het project af te ronden en alle taken van ’to do’ naar ‘done’ te krijgen. Binnen het Scrum framework wordt er niet vanuit gegaan dat de werkvoorraad continu wordt aangevuld.
Is een kanban-bord hetzelfde als een Scrumbord?
Hier is geen eenduidig antwoord op te formuleren. Het is natuurlijk niet exact hetzelfde, anders had het wel dezelfde naam gehad. De borden lijken van een afstand best op elkaar. Ze zijn in kolommen opgebouwd, waar de werkvoorraad doorheen beweegt.
In de toepassing van de borden zitten nog wel wat verschillen. Zo zijn de taken op een scrumbord volledig gericht op het scrumteam wat er mee werkt. Een kanbanbord brengt een geheel werkproces in kaart en kan dus team-overschrijdend zijn. Verder is het binnen Scrum heel gangbaar om prioriteiten te geven aan taken. Het team – of in sommige gevallen de Product Owner – bepaalt welke taken het meest urgent zijn en deze worden als eerste door het team uitgevoerd. Kanban kent dit principe niet, alles heeft dezelfde prioriteit.
De verschillen tussen een kanbanbord en een scrumbord zijn soms nog wel wat arbitrair. Uiteindelijk is het een middel om het werk te visualiseren, teams focus te geven en continu verbeteren te stimuleren. Welk bord dan daar precies bij gebruikt wordt, maar dan eigenlijk niet zoveel uit. Zolang de teams er goed mee kunnen werken en de doelen realiseren is het doel bereikt.
Vandaag nog zelf starten
Dat is niet zo moeilijk! Pak een vel papier of een whiteboard, maak 3 kolommen en je hebt de eerste aanzet voor Kanban al staan. Deze hele basale vorm van Kanban kan in heel veel gevallen ontzettend goed werken. Bijvoorbeeld om jouw eigen werk te structureren. Of om projecten als een verhuizing te plannen en uit te voeren.
Het geheel wordt wat complexer als er meerdere teamleden bij komen kijken of als de processen groter worden en voor een deel buiten het eigen bereik liggen. Ook in die gevallen kun je waarschijnlijk al zelf een start maken met de toepassing van Kanban. Maar de kans is groot dat je sneller vooruitgang boekt als een expert hier met je meekijkt. Hij of zij kent de complexiteit van processen en de meest gangbare valkuilen voor de toepassing van Kanban.
Meer weten over Kanban?
Wil je meer weten over deze methode, hoe dit het beste kunt toepassen in jouw werkomgeving of hoe je er meer over kunt leren? Bekijk dan één van onze lean trainingen of neem contact op met ons via: 020 – 345 3015 of contact@upd.nl.